The Role of Welding Consultants in Defect Prevention
Welding consultants bring a wealth of expertise to the table, helping businesses minimize defects and improve the overall quality of their welding operations.
From process assessments to training and inspections, their role is critical in achieving stronger, safer, and more efficient welds. And most importantly, compliant with Jurisdictional requirements.
Assessing Welding Processes
Consultants analyze existing welding processes to identify inefficiencies, inconsistencies, and potential sources of defects. This assessment lays the foundation for improvements that enhance weld quality and reduce errors.
Developing and Optimizing WPS
Welding consultants design and refine Welding Procedure Specifications tailored to the unique needs of each project, such as:
- Selecting appropriate welding processes and materials
- Determining optimal heat input and travel speed
- Defining joint design and preparation requirements
- Establishing preheat, interpass, and post-weld heat treatment parameters
- Specifying shielding gas type and flow rates
By aligning WPS documents with industry standards and project goals, they help minimize common defects which then has the benefit of improving performance.
Training and Certification
Skilled welders are the key to preventing defects, and consultants play a crucial role in training teams to follow best practices. They also guide certifications, ensuring welders have the qualifications needed to meet a projects welding requirements.
Monitoring Weld Quality
Consultants may oversee welding operations to verify compliance with WPS and identify issues early. Their expertise helps maintain consistent quality throughout a project, reducing the risk of defects and costly rework.
Testing and Inspection
By conducting thorough testing and inspections, welding consultants detect hidden flaws that might not be visible during production. These checks help ensure that welds meet safety and performance standards before moving to the next stage.
Analyzing Failure Causes
When defects or failures occur, consultants investigate their root causes to prevent recurrence. By identifying contributing factors, they provide actionable recommendations to improve processes and materials.
Cost-Reduction Strategies
Defect prevention often leads to significant cost savings, and consultants develop strategies to optimize resources, reduce waste, and minimize rework. Their insights help businesses achieve long-term efficiency while maintaining high standards of quality.
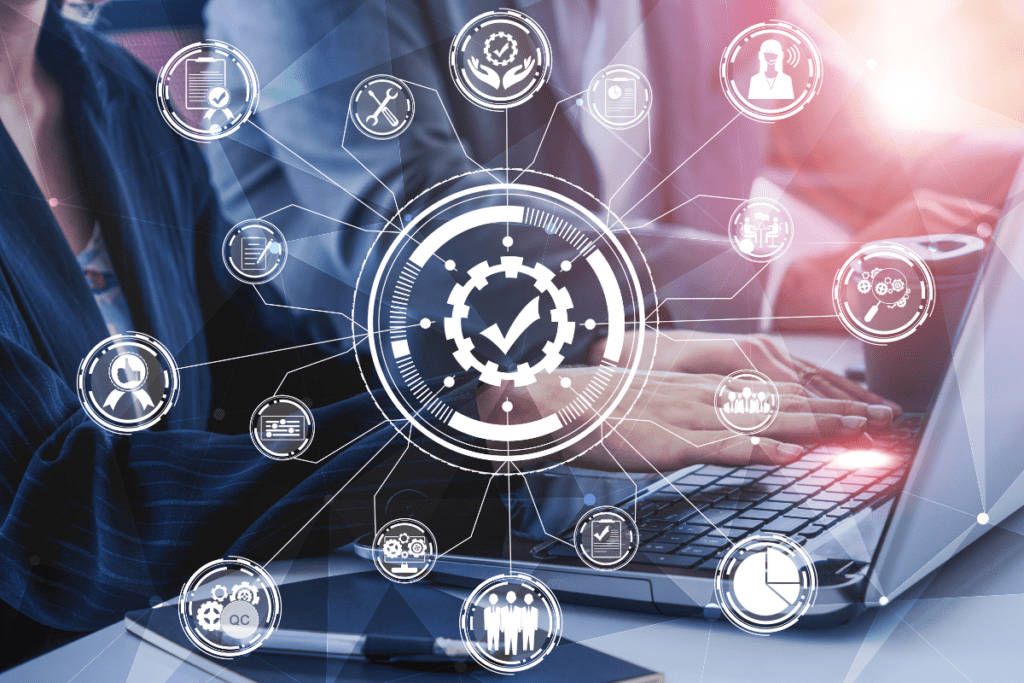
Avoiding Defects: WPS Development and Welding Consulting
Choosing the right partner in welding and materials engineering is essential for ensuring the integrity and success of your projects.
At Qualimet, our dedication to quality and our industry-leading qualifications enable us to provide customized solutions across various industries.
With continuous monitoring, expert support, and a focus on defect prevention, we help your projects meet the highest standards of safety and reliability.
Welding consultants play an important role in Public Safety by improving welding quality and preventing defects. Their expertise includes process assessment, developing and optimizing Welding Procedure Specifications (WPS), training and qualification, monitoring and inspection, and analyzing failure causes. These activities contribute to improved quality, cost savings, compliance with industry standards, and ultimately improving project outcomes, all for the benefit of stronger, safer, and more efficient welds.
Contact us to discover how our customized solutions can elevate your operations.
This information is provided by Qualimet for informational purposes only and is not intended to replace professional knowledge or consulting services. Although efforts have been made to ensure the accuracy and completeness of the information, Qualimet does not provide any warranties, express or implied, regarding the content. Users should seek professional advice and consultation for specific applications and requirements.