Common Welding Defects and How WPS Can Prevent Them
Welding is a critical part of countless industries, and even the smallest defect can compromise the integrity of a project.
Understanding common welding defects and how Welding Procedure Specifications (WPS) address them is key to achieving consistent, quality results.
By following a compliant WPS, you may minimize errors, boost efficiency, and sustain the quality requirements for your work.
Common Welding Defects
Welding defects are more than just surface issues—they can weaken joints, compromise safety, and lead to costly rework.
Below, some of the most common welding defects are covered, detailing their nature, causes, and potential dangers:
Porosity
Small holes or cavities form in the weld metal when trapped gas fails to escape during solidification. This issue often stems from contaminated base metals, improper shielding gas, or excessive moisture in the welding environment.
Porosity generally weakens the weld’s structural integrity, making it prone to cracking and failure under stress.
Cracks
Fractures in the weld metal, heat-affected zone (HAZ), or base material can form due to rapid cooling, excessive heat input, or high levels of stress during welding.
These cracks are especially dangerous because they may compromise the weld’s load-bearing capacity and when present can propagate over time, possibly leading to catastrophic failure.
Undercut
This defect occurs when the base metal adjacent to the weld is melted away, creating a groove along the weld’s edge.
It is often caused by improper welding techniques, excessive heat input, or incorrect electrode angles. Undercut generally reduces the weld’s strength and can act as a starting point for cracks under load.
Lack of Fusion
Lack of fusion happens when the weld metal fails to bond properly with the base material or previous weld passes. This issue usually arises from insufficient heat, improper technique, or contamination.
It creates weak spots in the weld, significantly reducing its load-bearing capacity and increasing the risk of failure.
Incomplete Penetration
This defect occurs when the weld metal does not penetrate the joint’s full thickness. It is often caused by low heat input, improper joint preparation, or incorrect welding parameters.
Incomplete penetration leaves unbonded areas in the joint, compromising its overall strength and durability.
Slag Inclusions
Non-metallic particles become trapped in the weld metal, preventing proper bonding between layers. Slag inclusions are commonly caused by improper cleaning between passes, incorrect electrode handling, or poor welding technique.
These inclusions may weaken the weld and may lead to cracking under stress.
Overlap
Excess weld metal flows onto the base material without fusing properly, creating a raised edge. This defect typically results from excessive deposition or improper welding angles.
Overlap may create stress concentrations and may lead to cracking or other structural issues.
Spatter
Molten metal droplets are ejected during welding and adhere to the surrounding surfaces, creating an uneven and messy finish.
Spatter is often caused by incorrect welding parameters, poor technique, or issues with shielding gas. While primarily aesthetic, excessive spatter may weaken the weld and increase cleanup time.
Distortion
Uneven heating and cooling during welding cause the base material to warp or deform. Distortion is often due to improper heat control, inadequate fixturing, or incorrect joint design.
It can result in misaligned components, requiring significant rework to correct.
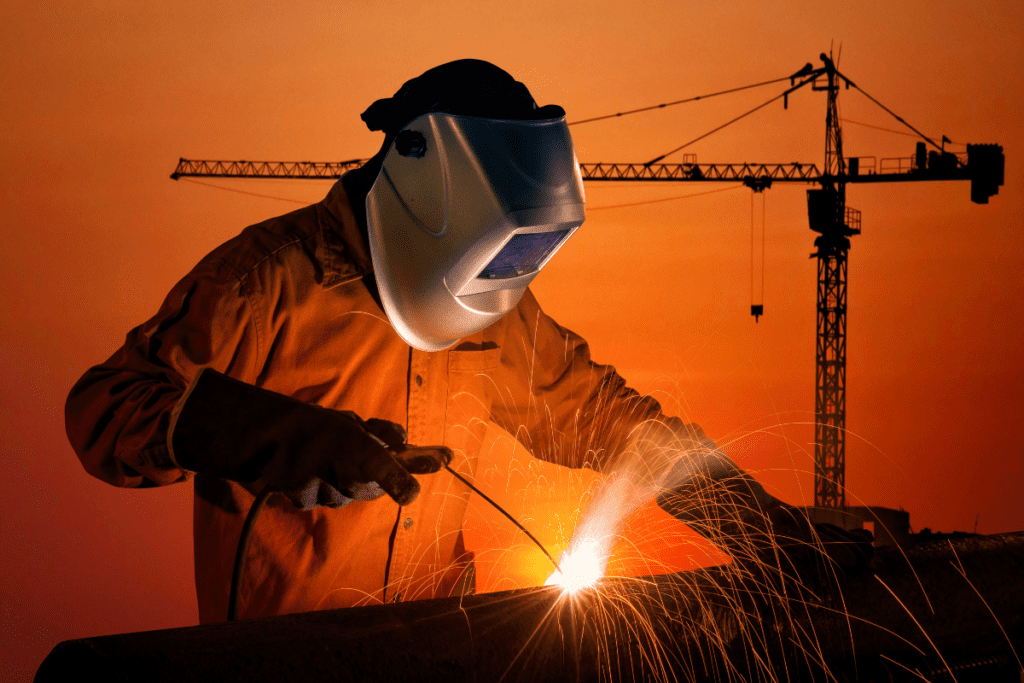
How WPS Can Prevent Welding Defects
Welding Procedure Specifications (WPS) is one of a number of essential tools for managing or mitigating risks such as defects and improving the overall quality of welded joints.
They provide guidelines to help welders avoid issues and achieve reliable results.
Standardizing Processes
A WPS provides a consistent set of guidelines for each weld, by following these guidelines, team members are more likely to meet your quality requirements.
This standardization is intended to reduce variability and minimize the likelihood of errors caused by inconsistent techniques or methods.
Controlling Parameters
WPS documents define critical parameters such as:
- Heat input: Controls the amount of energy applied during welding, directly affecting penetration and material properties.
- Travel speed: Determines the speed at which the welding torch or electrode moves, influencing weld size and heat distribution.
- Shielding gas flow: Protects the weld pool from contamination by creating a stable environment around the arc.
Monitoring these variables helps reduce defects like porosity, undercut, and incomplete penetration, resulting in stronger, defect-free welds.
Material Compatibility
Material selection and preparation are integral parts of a WPS.
A WPS specifies compatible base metals, filler materials, and preheating or post-weld treatments to support the reduction of issues such as cracks, distortion, and lack of fusion due to mismatched materials.
Consistent Quality
A well-developed WPS provides clear, step-by-step instructions for each joint type and welding position. This consistency allows for quality welds, minimizing defects and rework.
Improving Efficiency
By adhering to a compliant developed plan, welders are more likely to execute their tasks with efficiency, thereby reducing the necessity for trial and error.
This may result in earlier project completion, minimizing interruptions due to defects or rework, and efficient resource utilization, all while upholding quality standards.
Welding Procedure Specifications (WPS) are essential for preventing defects and ensuring quality workmanship. Following a compliant WPS helps welders reduce errors, improve efficiency, and maintain consistent quality, leading to faster project completion and less rework. For companies, a relevant WPS results in fewer defects, better safety, and lower costs from reduced rework and material wastage. By standardizing instructions and controlling key parameters, WPS ensures stronger, defect-free welds, enhancing resource efficiency and quality standards.
Although possessing a compliant Welding Procedure Specification (WPS) with all necessary essential variables is critical, it alone does not guarantee success. Equally important are proper training and adherence to correct techniques for preparation and welding. Without skilled welders who rigorously follow the prescribed methods, even the most meticulously defined WPS cannot avert defects or assure high-quality workmanship. Thus, investing in comprehensive training and emphasizing the importance of proper techniques are vital to achieving the desired outcomes in welding projects.
This information is provided by Qualimet for informational purposes only and is not intended to replace professional knowledge or consulting services. Although efforts have been made to ensure the accuracy and completeness of the information, Qualimet does not provide any warranties, express or implied, regarding the content. Users should seek professional advice and consultation for specific applications and requirements.