What is Welding Engineering?
Welding is the “spark of innovation” in engineering – the art and science of joining materials to create structures that withstand the test of time.
From towering buildings to intricate pipelines, welding forms the backbone of every structure.
At the heartbeat of many industrial endeavors, welding engineers and welding consulting in Edmonton ensure that projects are completed with integrity and in compliance with rigorous standards.
Let’s take a look at how welding works in the world of engineering and how welding engineers make it all happen:
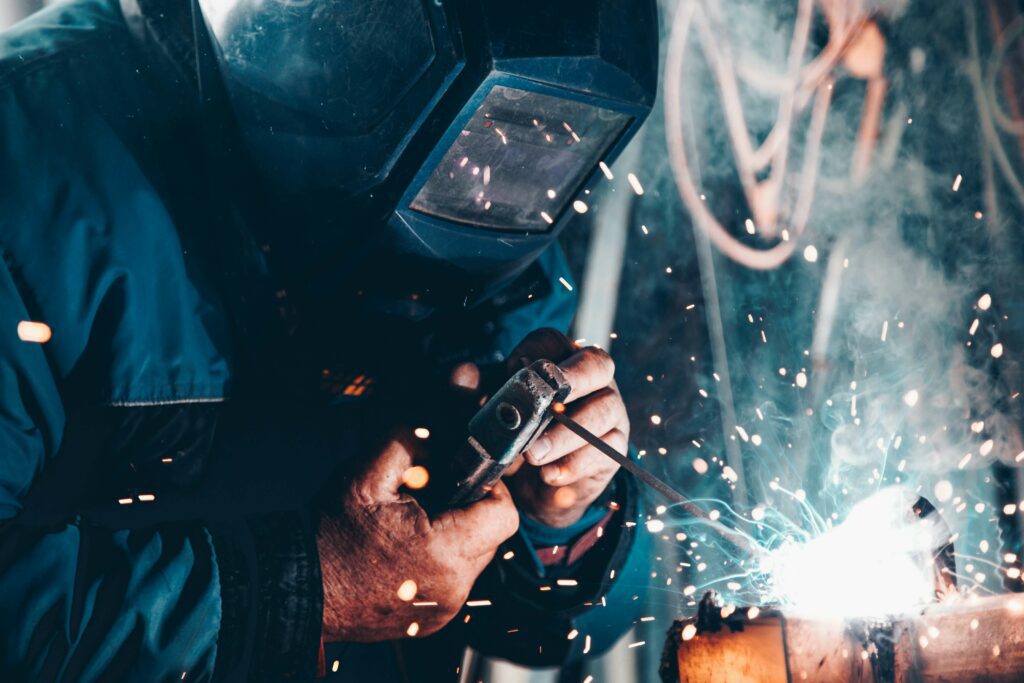
Photo by Christopher Burns on Unsplash
Understanding the Basics
Welding is a fundamental process in engineering that involves joining materials, typically metals or thermoplastics, through fusion.
Different welding processes exist, including:
- Arc Welding: Utilizes an electric arc to melt and join metals, commonly used for construction and fabrication.
- Gas Welding: Uses a flame produced by burning a fuel gas with oxygen to weld metals, suitable for both ferrous and non-ferrous materials.
- Resistance Welding: Joins metals by applying pressure and passing current through the materials, ideal for high-speed production and automation.
These processes use heat to melt the base materials, which then cool and fuse together to form a strong bond. Understanding these methods is important for welding engineers when it comes to choosing the best approach for a particular project.
Welding Engineering vs. Welding Technician
Welding engineering and welding technician roles differ significantly in their educational requirements and responsibilities.
Welding Engineering
Welding engineers typically hold a bachelor’s degree or higher degree in materials or mechanical engineering or a related field. This equips them with advanced knowledge in metallurgy, materials science, and engineering principles.
They often pursue certifications such as Certified Welding Engineer (CWE) through the Canadian Welding Bureau to validate their expertise.
The roles and responsibilities of a welding engineer include:
- Designing Weldments: Welding engineers are tasked with designing weldments, determining optimal joint configurations, weld sizes, and placement for structural integrity and performance.
- Developing Welding Procedures: They develop welding procedures, considering factors like material compatibility, joint accessibility, and desired weld characteristics to ensure efficiency and quality.
- Ensuring Compliance: Welding engineers ensure compliance with industry standards and codes, verifying that welding processes meet regulatory requirements and project specifications.
- Quality Assurance: They oversee quality assurance processes, conduct welding inspections and non-destructive testing, and maintain meticulous records to uphold quality standards.
Welding Technician
On the other hand, welding technicians typically undergo vocational training or associate degree programs that focus on practical skills and techniques.
Welding technicians carry out important tasks and responsibilities:
- Executing Welding Tasks: Welding technicians perform welding tasks according to established procedures, utilizing their practical skills and knowledge of welding techniques.
- Assisting Engineers: They assist welding engineers in implementing welding procedures, providing support in setting up equipment, preparing materials, and monitoring process parameters.
- Conducting Inspections: Welding technicians conduct visual inspections of welds, identify defects and anomalies, and report findings to engineers for further evaluation.
Maintaining Equipment: They maintain and troubleshoot welding equipment, ensuring proper functioning and safety measures are adhered to during welding
What Does a Welding Engineer Do?
Now that we’ve explored the differences between technicians and engineers, let’s take a closer look at what welding engineers do:
Designing Weldments
Welding engineers play a crucial role in designing weldments, which involves determining the optimal joint configurations, weld sizes, and placement for structural integrity and performance.
They analyze mechanical properties, stress concentrations, and thermal effects to develop robust designs that meet project specifications and safety standards.
Developing Welding Procedures
Welding engineers are responsible for developing welding procedures that establish the guidelines and parameters for executing welding tasks.
This involves specifying welding techniques, equipment settings, pre- and post-weld treatments, and inspection criteria to ensure consistent quality and compliance with industry standards.
By carefully documenting these procedures and conducting qualification tests, they validate the integrity and reliability of the welding processes.
Selecting Appropriate Welding Processes and Materials
Selecting the right welding processes and materials is crucial for successful welding projects.
Welding engineers assess factors such as material compatibility, joint accessibility, desired weld characteristics, and production efficiency to recommend suitable methods and consumables.
They consider the application environment, cost constraints, and quality requirements to make informed decisions that optimize performance and durability.
Overseeing Welding Operations
Welding engineers oversee welding operations to ensure adherence to approved procedures, quality standards, and safety protocols.
They collaborate with technicians and welding personnel to troubleshoot issues, monitor process parameters, and implement corrective measures as needed.
By maintaining meticulous records and conducting inspections, they mitigate risks and uphold project integrity throughout the fabrication process.
Collaborating with Multidisciplinary Teams
Effective collaboration with multidisciplinary teams is essential for welding engineers.
They work closely with design engineers, materials specialists, quality assurance professionals, and project managers to integrate welding processes seamlessly into overall project objectives.
By having open communication and sharing technical insights, they facilitate innovation, problem-solving, and continuous improvement initiatives.
Ensuring Quality and Compliance
Welding engineers are responsible for ensuring the quality and compliance of welded components with industry standards, codes, and regulations.
They do this by:
- Developing and Implementing Quality Assurance Plans: These plans encompass inspection protocols, documentation requirements, and corrective action procedures to maintain high standards throughout the fabrication process.
- Conducting Weld Inspections: Welding engineers use various inspection techniques, including visual inspection, ultrasonic testing, radiographic testing, and magnetic particle inspection, to assess weld quality and structural integrity.
- Performing Non-Destructive Testing (NDT): Welding engineers utilize non-destructive testing methods such as radiographic testing, ultrasonic testing, penetrant testing, and magnetic particle testing to evaluate welds without causing damage to the components.
- Staying Up-to-Date with Evolving Technologies: Welding engineers stay abreast of advancements in welding technologies, materials, and inspection methods to enhance quality and efficiency continually.
By using these measures and continuously improving their practices, welding engineers play a vital role in upholding quality standards, ensuring regulatory compliance, and contributing to the overall success of engineering projects.
Elevate Your Projects with Qualimet
When it comes to welding consulting in Edmonton, Qualimet is here to deliver excellence and reliability to your project.
We are committed to quality and are here to provide you with unparalleled weld quality and help you remain compliant with industry standards.
Contact us today to elevate your projects to new heights of success!
Industry News
Welcome to a Year of Possibilities
Welcome to a Year of Possibilities Hello friends, Let’s make 2025 a year to remember. As we move forward, I’m reaching out to share how…
White Paper 4: Addressing the Training Gap in Alberta’s Construction Industry
Introduction The construction industry in Alberta faces a significant training gap, with a need to recruit and train nearly 27,700 additional workers by 2027. This…
White Paper 3: Enhancing Welder Training and Competency
Introduction The construction industry relies heavily on skilled welders to ensure the quality and safety of projects. However, a gap in welder training can lead…